上光油的成膜机理
上光油的成膜机理
在包装印刷行业中,为了提高包装印刷制品的高附加值,运用印后覆膜和表面涂饰(喷或印)上光油等整饰技术,经流平、干燥压光后在印品表面形成薄而均匀的透明光亮层,其机理就是利用印刷品画面特性的主体反射光和印刷品的表面性能的表面反射光以其质的提升去弥补包装印刷制品前期中的不足。目前,因上光加工整饰工艺涉及的因素很多,例如包装印刷承印材料、油墨、光油、原料(含粘着力、粘度、表面张力等)、上光生产工艺的环境条件(主要是高温、高湿的梅雨季节),都可能会引起印品上的底油与面油的离皮、甚至表面上光后的雾状故障,并导致该制品的报废,引发了整饰技术的失衡。造成这种故障的原因是:
1、上光的目的:
生产和使用底油和面(光)油的目的是为了得到复合需要的涂布光油薄膜,其成膜的过程直接影响着上光油能否充分发挥预定的效果,以及能否得到上光油在涂饰中表现出来的经济、耐用、方便。上光油的成膜包括光油涂布(喷、涂、印)在包装印刷承印物表面,使其形成固态(体)的连续的光油薄膜两个过程。目前流行的整饰上光方式:先打底油(醇溶型或水溶型),再上UV油。其整饰工艺几乎涵盖了纸制品,甚至软包装制品领域。当然,在涂饰光油过程中可以决定得到上光油薄膜层的机械、光学等性能。对于底油、面油两种截然不同固化干燥形态和性质的成膜性能,如何选择正确、合理的操作生产工艺技巧,在保证质量的条件下,既不影响后加工过程时质的变化,又能得到最佳的整饰艺术效果才是最终目的。
2、成膜的机理:
市场上售出的底油和面油均属于液体(态)的连结上光油,当上光油在包装印刷制品表面时,仅只完成了涂饰上光的第一步。因为液体光油的“湿膜”变成了干膜,是上光油必然要发生的形态变化过程,即从能流动的液体(态)逐步变为不易流动的液体(态)。这种一系列变化也是学术界定义的流动性或粘度的变化。液体底油或上光油在整饰加工中,粘度约在0.03-0.07Pa.s之间。因此,液体光油涂布在包装印刷制品表面后,开始得到的“湿膜”的粘度是很低的。而要成为具有一定机械性能的“干膜”时,即人们常常所说的底油或面油的“全干”阶段时,这时粘度至少要达到10Mpa.s以上。从“湿膜”到“干膜”的粘度变化过程中,可以这样认为:任何一种液体(态)的底油或光(面)油的干燥或固化过程必然都要经过该产品粘度的变化过程,即是固体(态)的底油或光(面)油,由于其本身多为粉末状,但在整饰粘附在被涂布的包装印刷制品表面后,还不可能立即就形成连续进行变成为固体(态)连续光油薄膜的过程,只有达到一定条件才能完成全部的由光油涂布到干燥成膜的过程。
3、产生光油薄膜雾化因素:
正常情况下,上光油一般不会产生雾化,例如用户在香烟盒表面往往在表面再覆一层聚烯烃薄膜后,当湿度大特别是气温高到一定条件时,当底油涂布后,面油往往因极短暂的气雾致使光油附着牢度不好,而覆在上光油表面的聚烯烃薄膜就会出现浓浓的均匀的雾状小蒸汽,这时反而降低或导致商品品牌的内质变化。
液体光油被涂布在包装印刷制品表面后形成可流动的液体(态)薄层,一般成为“湿膜”。它主要按照不同机理,通过不同方式(红外线干燥盒紫外线光固化干燥)变成固体(态)的连续“干膜”。这才能得到需要的涂布上光油膜层。这个由“湿膜”变成“干膜”的过程通常称为“干燥”或“固化”。这就是我们常说的干燥或叫固化干燥的过程时底油和面(光)油涂饰后成膜过程的核心阶段。这是因为它液发生形态的变化/即从分散的粒子凝集为连续光油涂膜才能实现成膜的过程。无论底油、光油还是固体(态)底油或光油,常被称为“干燥”或“固化”的过程的干燥速度都是由光油本身组成结构、成膜的条件(包括温度、湿度、油膜厚度等)和被涂饰的包装印刷制品的材质,尤其是水分含量多少特性决定的。
不同形态和组成底油、光油有各自的成膜机理,成膜机理是由整饰材料所用的成膜物质的性质决定的,比如底油的成膜可以定义为物理成膜方式——即溶剂或分散介质的挥发成膜,而UV面油的成膜可以定义为化学成膜方式——即利用紫外线照射引起光油的聚合反应而进行干燥的高聚物的成膜过程。前者常又分溶剂型或分散型两种类型,但底油在成膜过程中必须经过一种形式,例如非转化型的底油,在被涂布后的“湿膜”中的溶剂或分散介质随着挥发到大气中,从而使粘度逐步增大至一定程度而形成固体(即就完成了底油成膜的全过程)。如果是转化型的底油在溶剂或分散介质的挥发同时再用化学方式成膜,这种成膜方式是液体底油或分散型底油里生产的逆过程。
总之,底油涂膜的干燥速度和干燥程度直接与所用溶剂或分散介质的挥发能力相关联,同时也与溶剂(包括水)在油膜中的扩散程度,以及成膜物质的分子结构、分子量、玻璃化温度有关。例如:先大多选用的热塑性丙烯酸树脂为主体的底油以溶剂挥发方式成膜,难免在液态变为固态过程除了包装印刷承印物水分外,或多少的仍会残留多少不等的溶剂物。另外,聚合物粒子凝聚成膜,这种底油的成膜方式是依靠其中作为成膜物质的高聚物粒子在一定的条件下互相凝聚而成为连续的固体(态)光油膜层。这是分散成型底油能的成膜方式。含有可挥发的分散介质的分散型底油,如乳液的底油非水分散型的底油以及有机溶胶等,当分散介质挥发的同时产生聚集而形成连续的光油膜层。
如果是转化型成膜物质组成的,那就在以化学方式形成底油涂膜。而目前“水溶性底油”的成膜也是依靠聚合物粒子凝聚为主要的成膜方式,而塑性溶胶由于含有不挥发的分散介质,其成膜是通过分散介质中的高聚物粒子溶胀、凝聚、成膜。通常情况下,固体底油在受热条件下通过高聚物粒子的热熔、凝聚而成膜,热固性树脂组成后还要经过化学反应方式才能成膜这个过程的。后者的UV光(面)油通常称为化学成膜方式。化学成膜以遵循高分子合成反应机理分为链锁聚合反应成膜和逐步聚合反应成膜两种类型。
目前,应用在包装印刷制品上的UV光油,除氧化聚合物形成外,一般采用引发聚合和能量引发聚合两种形式(均称为光敏树脂,即光油体系的光敏树脂在紫外线照射下树脂发生聚合反应形成的光油薄膜,称为紫外线固化上光油)。引发聚合是将典型的不饱和聚酯树脂液体光油依靠引发剂聚合成膜,其机理是利用该材料含有不饱和的基团,当引发剂分界产生链式反应而形成大分子的面膜。
常被包装印刷整饰技术看好的是能量引发聚合形式,其主体多选用价廉的环氧丙烯酸树脂等。这种利用该材料含有的共价键通过能量引发聚合形式而形成光油面膜。这是因为共价键均裂需要较大的能量,故选择了采用紫外光线的辐射能引发的主要形式之一。为此人们通常称为光固UV光油。该材料在光敏剂的存在下,光油的成膜物质的自由基加集反应进行得非常迅速,可在几分钟甚至数秒内固化成膜。还有利用电子辐射成膜光油称为电子固化光油。由于能直接激发含有共价键得单体或聚合物生成自由基,所以能在数秒得时间内完成加集反应固化成膜。所以说电子束固化光油是目前包装印刷制品整饰工艺技术中成膜中能量引发聚合形式之一。
纵观上面已叙述的底油和光(面)的材料、成膜机理,我们就会发现上光油体系采用易乳化的树脂作为光油成膜物质材料,当光油生产、贮存和使用过程中由于气温的上升或湿度大时,商品及包装内的水蒸汽就会不断凝结于顶层的聚乙烯薄膜的内表面,生成极多的微细水珠,形成一层不透明的雾状白色水膜,而使透光性大大下降,随着膜内的温度会上升,已经乳化的酸性水分导致了上光油的不稳定性,释放出白色雾状气体,从而影响包装印刷后涂布的UV油材料的表面性能。严重时,造成用户对包装印刷品的降价退货,甚至被起诉索赔。
4、防止上光油墨和聚烯烃气雾的方式方法:
面对气雾故障,要明确认定一点,即气雾是光油薄膜和聚烯烃薄膜的缺陷造成的,甚至可以延伸到包装印刷承印物含过多水分造成的。根据经验解决的方法是:
第一,在上光油或聚烯烃薄膜体系加入防雾剂充分利用防雾剂的表面活性作用,使上述材料变为亲水性,生成的微细水珠在光油薄膜或聚烯烃薄膜表面逐渐凝结成大的水滴,使水滴沿着薄膜向下流或再回流到包装印刷制品内,甚至商品内,从而恢复薄膜的透明性,将上光油、聚烯烃薄膜通过防雾剂的作用机理——(1)利用亲水高分子材料;(2)交联助剂;(3)表面活性剂由它们去吸收湿气。不仅能预防和抑制包装印刷制品起白霜雾化这一严重故障,还能大大地增加上光油、聚烯烃体系里树脂的耐水性和抗摩擦性。软包装聚烯烃薄膜材料再加防雾剂的同时,建议添加微量的成核剂,以提高薄膜的透明性。
第二,(1)用户尽可能将包装的商品贮存在通风干燥的仓库里;(2)根据溶剂(或水溶剂)的不同挥发速率,设计一个能挥发梯度平衡而又流得平整的上光油制品或油墨制品,从而使上光油的溶剂残留量降低到最小值;(3)在上光油体系加入能封闭水分释放得蜡质材料;(4)将隔热、耐热的云母粉或有机硅树脂引入上光油体系,以降低在气温上升时包装印刷承印物的稳定性;(5)选择含水量少或PH值小的包装印刷涂饰承印物。(6)在光油体系增添催化剂(如氧化亚锡),以提高光油成膜后的透明硬度值。
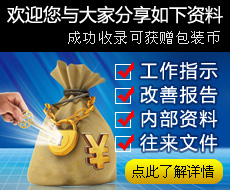