如何检测和控制PS版表面处理液(二)
如何检测和控制PS版表面处理液(二)
目前,国内PS版生产企业的表面处理液检测和控制的现状大致可以分为人工控制、半自动化控制和自动控制。
1)人工控制
这是我国目前大多数中小型PS版生产企业的普遍做法。主要表现在整个生产线的数据化管理系统尚未形成,自动化程度低,对于表面处理工艺段的各种酸碱处理液的检测往往是只有仪表显示,而无自动化的实时回控。其中浓度检测是由人工实验室滴定完成的,补加液也是由人工凭经验进行,因此受人为因素影响很大。
① 定时巡检。在生产线上,表面处理工艺段的各个酸碱溶液的储液箱中,各自配备有相应的酸碱浓度检测仪器,有盒式的或是壁挂式的显示盘,显示箱中酸液或是碱液的实时浓度。在正常生产的过程中,随着反应的进行,各种酸碱溶液的浓度都会不同程度的降低或变化,因此工人会按照一定的班次,定时巡查各个仪表的示数。定时检查后,工人会通知检验人员取样检测处理液的实际浓度。此外,如果在生产过程中有问题出现而影响成品版材质量时,工人也会将表面处理液取样送检。
② 实验室滴定检测。溶液的浓度检测是在实验室通过滴定的方式完成的,检验员根据指示剂的颜色变化确定滴定终点,然后根据标准溶液消耗的体积计算分析结果,得出处理液的准确浓度。
③ 人工补加。负责补加原液的工人在得到检验员的补加通知后,根据相应的浓度差值,向处理箱中补加一定量的原液,以恢复工艺要求的溶液浓度。具体补加原液的量往往是凭借工人多年的实践经验,逐步摸索出来的一定的经验数值。
2)半自动化控制
目前,一些企业在基于人工控制的基础上,设计出一套"半自动化"的溶液浓度控制装置。
在生产线上,各表面处理液循环槽中均配备有相应的酸碱浓度检测仪器,通过导线连接有外置的显示面板,实时显示循环槽中酸液或是碱液的浓度值。与此同时,有管道从原液储罐通向处理液循环槽中,由阀门控制一定的液体流出的量,连续地向处理槽中滴加原液,以维持槽中处理液浓度的稳定。
原液的实时滴加量是工人凭借多年实际生产经验摸索出来的,配合不同车速条件和生产条件,逐步形成了一套经验数据,一般以"滴/分钟"来计量和控制。
3)自动化检测与控制
目前,国内外的一些大型PS版生产企业均采用处理液浓度自动化检测系统,使用计算机控制和显示,实现了溶液浓度的自动检测和原液的自动补充。此类系统采用先进的酸液浓度传感器、酸液温度传感器及相应的智能仪表,在线检测各段表面处理液的浓度和温度,通过自动控制药液浓度及温度的接口与计算机总控制柜相连接,将检测结果传送至中央控制器进行计算处理,再由控制器发出控制指令,驱动耐酸、耐碱电磁阀,控制盐酸、硫酸以及除油段碱液等处理液的自动补加,从而达到对表面处理液浓度、温度的自动控制。由于自动化控制的实时性和准确性较高,很好的保证了版基砂目质量以及氧化膜层质量的稳定性。
现有检测控制系统存在的问题
1)人工控制及半自动化控制系统存在的缺点
目前,我国国内的中小型PS版生产企业的生产线表面处理溶液的浓度普遍以人工控制为主,整个生产线的数据化管理系统尚未形成,自动化程度相对较为低下,并且受人为因素影响很大,其缺点主要表现在以下几个方面。
① 存在时间滞后性。从工人定时巡检到通知化验员取样检测直到最终原液的补加,一般要耽误半个小时甚至一个小时的时间。在这个过程中,表面处理液的浓度得不到实时的控制,实际生产中的工艺条件早已发生了改变,必将影响版材的表面粗化处理的质量,从而影响最终的版材质量。
② 人为因素影响。首先,滴定操作为人工操作,在进行指示剂比对确定滴定终点时,势必会受到人为因素的影响从而影响检测结果的准确性;其次,在原液补加时也是由人工操作完成,不同的人会执行不同的经验标准,各个班次间的执行标准也不尽相同,从而生产工艺条件得不到稳定一致的控制。
③ 消耗酸碱。滴定检测中需要使用标准酸碱溶液,随着生产线长年的运转,必然增加了原料消耗,提高了生产成本。
④ 占用人力资源。由于滴定检测由人工操作完成,因此每个班次都要配备专职的检验员,从而增加了人工费用的支出,提高了生产成本。
半自动化控制采取了实时滴加原液的方法,在一定程度上弥补了人工控制存在“时滞”的缺陷,但是实时补充的量也是凭借多年生产经验而确定的,在准确性上难以得到保证。此外,半自动化控制也包括检测环节,因此也存在着人为因素的影响和标准酸碱溶液的消耗等。
2)自动化控制系统的难点
目前,尽管国内的一些中外合资的大型PS版生产企业已经应用了自动化的检测与控制装置,但是整套系统的开发与设计还没有实现国产化,一般是由外方确定工艺条件及具体的控制要求,由国内的专业厂家完成相应控制系统的硬件设计,控制软件一般也由外方实施设计。因此,对于自动化控制系统的相关技术资料和控制系统设计的关键问题,各企业均持对外保密的态度,给自行开发研制该控制系统带来了一定的难度。
PS版制造过程中表面处理液检测与控制系统的研发
1)研发课题内容
目前,我们的课题是自行研制开发一套基于PLC的PS版生产线表面处理液浓度和温度的自动化检测与控制系统,实现其国产化。该系统能实现PS版生产线表面处理段各种酸碱处理液的浓度和温度的实时自动检测,通过中央控制单元分析和计算,控制执行单元进行原液的补加回控和温度的控制。从而达到生产线化学段浓度和温度的自动控制,实时而准确地维持表面处理段的工艺条件,从而很好的保证版基砂目质量及氧化膜层质量的稳定性。
2)课题预期效果
根据设计的要求,该系统将实现生产线表面处理段工艺的完全数据化、规范化管理。生产现场将不设岗位工,只设巡检员,整套检测与控制系统将达到相当高程度的自动化。
当正常生产时,中控室可以监视检测与回控设备的运行状态及工艺参数的实时反馈情况,操作员负责定时观察记录数据,监测各设备的运转情况;当工艺条件需要改变时,由操作员通过人机界面输入新的工艺参数,并将控制命令发出,该命令信号通过网络系统快速传送到PLC的CPU,CPU将该信号与现场设备状态信号相结合,经过逻辑运算后将新的控制命令发出,使现场设备运行状况产生相应的改变,从而完成对工艺条件的调整;当生产现场发生异常情况时,要求中控室操作员能够及时发现,并在一定技术规范的指导下做出相应的处理。
预计该系统对溶液浓度的控制精度将达到±1%,对温度的控制精度将达到±1℃。
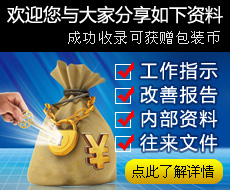